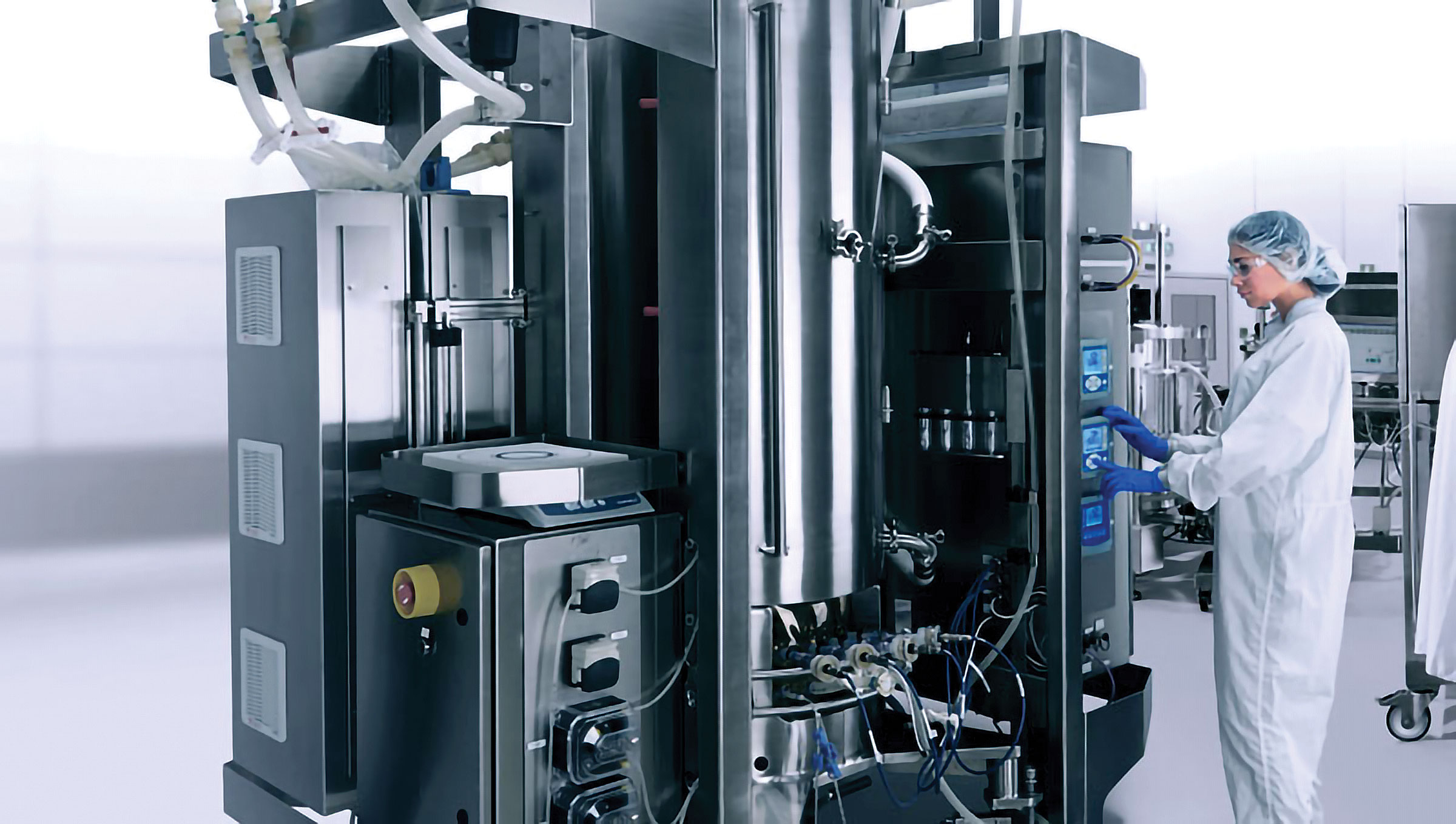
Products
Biomixing inside
BioMixing inside agitation and aeration technology that can be used to retrofit your current bioreactor.
Innovative bioreactors that can decrease the mixing time by up to 75% due to our efficient mixing and aeration system.
We work with our clients to offer customised turnkey projects, providing unique solutions for each case.
We offer customized high performance control systems for fermentation and related processes when standard or existing equipment won't suffice.